L’implementazione di Industria 4.0; vantaggi e criticità
La sigla “industria 4.0” rappresenta un cambiamento significativo sia sul piano tecnologico ma anche su quello dell’organizzazione del lavoro e delle competenze richieste per poter guidare lo stesso processo di cambiamento nel modo più efficace. Ci si può riferire ad un nuovo modello produttivo, basato sullo sviluppo delle tecnologie digitali, sull’interconnessione tra diverse componenti produttive e su un approccio orientato all’innovazione di prodotto e di processo. Non si tratta di uno scenario futuristico, ma di una realtà che sta investendo il mondo industriale a diversi livelli. I manager devono imparare quanto prima a far fronte ai cambiamenti in atto, considerando che anche la concorrenza si impegnerà a modificare le proprie strategie in modo altrettanto veloce.
Le aziende che vogliono restare al passo con i tempi devono adeguarsi ed investire in soluzioni tecnologiche che rendano più efficaci i processi e favoriscano modelli di lavoro più efficienti. In tal senso, si può affermare che industria 4.0 rappresenta una nuova frontiera della competizione globale.
Industria 4.0 viene ad interessare un’importante parte delle tematiche di ricerca e innovazione indicate come prioritarie per il futuro del settore manifatturiero del nostro paese. Un paese il nostro al quale è riconosciuta la capacità di integrare tecnologie innovative all’interno dei prodotti per fornire soluzioni ad alto valore aggiunto.
Nel piano nazionale industria 4.0 si parla di Industria 4.0 come la quarta rivoluzione industriale che consiste nella connessione tra sistemi fisici e digitali, analisi complesse attraverso Big Data e adattamenti real time; ciò con l’utilizzo di macchine intelligenti interconnesse e collegate ad internet. Grazie a complessi sistemi tecnologici che controllano le azioni dei singoli strumenti presenti nel processo produttivo è possibile organizzare virtualmente la produzione e, allo stesso tempo, che essa, con l’intervento di sensori che ne consentono un monitoraggio costante, si ottimizzi a seconda delle diverse esigenze e condizioni.
Il sistema 4.0 rappresenta un cambiamento significativo, come ricordato, non solo sul piano tecnologico ma anche nelle modalità di lavoro: digitalizzare l’azienda significa non solo acquisire nuove tecnologie ma attivare un processo di cambiamento che interessa la gestione dell’azienda; significa perseguire congiuntamente obiettivi di flessibilità, velocità, produttività, qualità, maggiore competitività dei prodotti. In altri termini, si può affermare che industria 4.0 non significa solo introdurre macchinari all’avanguardia dal punto di vista tecnologico, ma anche saper combinare diverse tecnologie in modo da integrare il sistema fabbrica e le filiere produttive interessate in un sistema connesso. Si tratta di un connubio tra cambiamenti tecnologici e conseguenti riorganizzazioni lavorative. L’impiego delle nuove tecnologie digitali è destinato a cambiare l’organizzazione produttiva e di mercato delle aziende e il modo stesso di lavorare. Saranno richieste, come sarà meglio specificato in seguito, maggiore flessibilità degli orari e delle prestazioni, lo sviluppo di nuove competenze e un livello più alto di coinvolgimento e di partecipazione dei lavoratori nei processi produttivi.
Lo sviluppo di industria 4.0, a conferma delle ricadute organizzative, richiede un’azione di snellimento dei processi, la riduzione di sprechi e di attività a non valore aggiunto.
L’innovazione 4.0 investe, in particolare, la possibilità di poter combinare diverse tecnologie e di integrare il sistema di fabbrica e le filiere produttive in modo da renderle un sistema integrato e connesso, in cui macchine, persone e sistemi informativi collaborano fra loro per realizzare prodotti, servizi e ambienti di lavoro più “intelligenti”. Un’azienda 4.0 deve essere in condizione di variare i piani e le modalità di produzione coerentemente con le variazioni della domanda o di tipologia di prodotto, in una logica di modularità e riconfigurabilità continua. Si può parlare della realizzazione di ambienti produttivi flessibili e riconfigurabili per realizzare piani e processi produttivi grazie alla disponibilità di modelli, dati e informazioni capaci di delineare configurazioni specifiche per le situazioni che di volta in volta si presentano. Essa sarà sempre più in grado di realizzare lotti di produzione molto ridotti, addirittura unitari. L’impiego efficiente delle risorse produttive potrà essere perseguito lungo l’intera supply chain e la catena del valore ne potrà beneficiare garantendo ritorni adeguati sia al cliente e sia ai diversi attori della filiera. Significativi sono gli effetti sulle forme di organizzazione del lavoro che dovranno dare delle risposte concrete allo sviluppo delle competenze professionali, del lavoro in team, della formazione continua, alla richiesta di un miglioramento della produttività.
Il modello di produzione industriale tende a diventare sempre più “personalized”, legato cioè alla capacità di progettare, produrre e commercializzare prodotti in base alle specifiche richieste del cliente. Le tecnologie digitali sono in grado di rendere disponibili una grande quantità di informazioni sui clienti, per cui è possibile definire con maggiore precisione i bisogni degli stessi attivando soluzioni dedicate, al limite appunto personalizzate per i singoli clienti, agendo di conseguenza sulla filiera produttiva per pianificare, nel modo più efficiente, le relative produzioni, in termini di personalizzazione e qualità dei prodotti con maggiore valore d’uso.
Effetti positivi sul piano competitivo possono derivare da una maggiore flessibilità ed una migliore capacità di risposta al mercato, da un passaggio più rapido dal prototipo al prodotto
Le nuove soluzioni tecnologiche possono, altresì, consentire di scambiare dati e informazioni in tempo reale sulle capacità produttive di un elevato numero di aziende; grazie a tali informazioni diventa possibile sia identificare nuovi partner e sia integrarsi maggiormente con i partners con i quali già si collabora in modo da ridurre i costi e i lead time.
In questo contesto le tecnologie digitali supportano l’integrazione dell’intera catena del valore dalla progettazione del prodotto, alla gestione della produzione, all’erogazione dei servizi post vendita.
Le catene del valore tendono ad essere sempre più interconnesse, integrate e proiettate sul mercato.
In questa trasformazione macchine, prodotti e sistemi collegati lungo una catena del valore che va al di là della singola azienda; sistemi interconnessi, capaci di interagire tra di loro, di auto-configurarsi per adattarsi ai cambiamenti.
Per il nostro paese si tratta di una significativa opportunità di rilancio del settore manifatturiero, noto in tutto il mondo come esempio di eccellenza e creatività.
Guardando all’innovazione manifatturiera degli ultimi anni, si può affermare che industria 4.0 si presenta più come un’evoluzione già in corso da alcuni anni, che come una vera e propria rivoluzione industriale abilitata dalla disponibilità di nuove tecnologie. Di certo, la disponibilità e la sempre maggior diffusione di tecnologie digitali abilitanti industria 4.0 forniscono nuovi strumenti di interconnessione delle risorse manifatturiere, determinando un’accelerazione del rinnovamento dei modelli di business, ciò considerando le aree tecnologiche ritenute strategiche per l’implementazione di industria 4.0 e cioè la robotica avanzata, il controllo e la supervisione avanzati dei processi produttivi, la fabbrica digitale, l’Internet of Things e i Big Data, la Cyber Security.
Cambiano i metodi di produzione, così come si trasforma il modo d’intendere i processi logistici di un’azienda.
Emergono due parole chiave fondamentali: interconnettività (disponibilità di informazioni sull’origine, la posizione e la destinazione delle merci da movimentare) e automatizzazione, che rappresenta l’evoluzione dell’automazione della terza rivoluzione industriale e dove la robotica vede potenziate le proprie capacità cognitive, le capacità di adattamento al contesto, la capacità di auto-apprendimento, la capacità di manipolazione avanzata. Importante è sottolineare che non è sufficiente adottare in modo isolato questa o quella tecnologia innovativa, ma è necessario attivare un’integrazione delle diverse risorse disponibili per riuscire a generare valore addizionale, riducendo le inefficienze. Alle due parole chiave indicate si possono aggiungere altri concetti in grado di qualificare le direttrici di cambiamento del sistema 4.0: la virtualizzazione che consente di ridurre i tempi e i costi del passaggio dalla fase di prototipazione a quella di produzione; l’interazione da remoto, nel senso di potere, a distanza, rilevare dati sul funzionamento o sulla necessità di introdurre correttivi riguardo le stesse macchine; la possibilità di realizzare elaborazioni e reazioni real time, ciò che significa la possibilità di raccogliere in tempo reale i dati di processo.
Ogni azienda sarà protagonista di un processo di cambiamento che coinvolgerà gli acquisti, il processo produttivo, le relazioni con il mercato, la formazione del personale.
I dispositivi elettronici messi a disposizione dai nuovi sistemi di fabbrica, i nuovi software che si occupano dell’immagazzinamento immediato dei dati all’interno dei database aziendali, l’impiantistica innovativa che permette la connessione tra la fisica e l’informatica in senso stretto e anche i novi metodi di comunicazione sono alla base dei cambiamenti che stanno attraversando in maniera trasversale i nuovi concetti di industria e di logistica.
Tale cambiamento si può manifestare in molteplici forme, ma trova nella possibilità di connettere oggetti tra loro, nella raccolta di enormi quantità di dati in tempo reale, nei processi di estrazione di informazioni anche automatica di tali dati le principali premesse tecnologiche.
Industria 4.0 tra origine da una sorta di convergenza di manifattura e servizi in molti settori industriali, dando luogo a veri e propri ecosistemi industriali in continua integrazione, contribuendo così a ridurre classiche divisioni settoriali; così come dalla nascita di nuovi modelli di business resi possibili dallo sviluppo dell’ICT.
In tal senso è importante ricercare una maggiore flessibilità di risposta ad ogni criticità lungo tutta la catena del valore.
L’industria 4.0 spinge a trovare soluzioni tecnologiche per ottimizzare i processi produttivi, supportare i processi di automazione industriale, nonché favorire la collaborazione tra imprese mediante una gestione integrata della logistica.
In tale contesto si presenta la seguente domanda: le macchine sono destinate a sostituire il lavoro umano oppure il futuro del lavoro dipenderà dal raggiungimento di un bilanciamento tra nuove generazioni di macchine e capacità umane?
L’introduzione di industria 4.0 e il clima di rinnovamento indotto nelle fabbriche stanno sicuramente cambiando i profili professionali dei lavoratori, con una riduzione delle attività manuali più tradizionali.
Quali competenze saranno richieste dallo sviluppo di industria 4.0? Come adattare di conseguenza i programmi formativi? Come la formazione può diventare la più importante risposta ad un mondo del lavoro in costante cambiamento?
Quali le ripercussioni sul mondo del lavoro?
Si possono individuare alcuni aspetti su cui riflettere: creazione di nuovo lavoro, trasformazione del lavoro (interfacce uomo/macchine intelligenti), eliminazione di posti di lavoro (conseguenza dei processi di automatizzazione), trasferimento del lavoro, ricerca di elevati livelli di flessibilità.
I cambiamenti apportati da “industria 4.0” sul mondo del lavoro, alla luce di alcune esperienze che vedono anche nel nostro paese già applicati alcuni di essi, potranno determinare un aumento del tasso di sostituzione dei lavoratori con le macchine?
In termini di ricadute sui posti di lavoro si possono rilevare due diverse osservazioni: da un lato si afferma che l’adozione di macchine sempre più guidate da sistemi informatizzati e di robot di ultima generazione avrà come ricaduta la necessità di lavoratori dotati di specifiche conoscenze professionali e adeguatamente formati. D’altro lato, esperti in materia lavoristica evidenziano il rischio di una drastica riduzione in prospettiva di tutte quelle attività che richiedono lo svolgimento di lavori ripetitivi. Ciò genera, inevitabilmente, notevoli preoccupazioni per tali lavoratori che vedono il cambiamento come una vera e propria minaccia in termini di rischio di perdita del loro posto di lavoro. Ciò potrà interessare non solo le attività produttive di tipo seriale, ma anche altri settori dove il lavoro manuale realizzato con gli attuali mezzi di produzione appare destinato ad essere sostituito dalle più moderne soluzioni tecnologiche. D’altro lato, le stesse tecnologie possono essere utilizzate per arricchire il ruolo dell’operatore, chiedendogli maggiore autonomia e competenza, rafforzandone di fatto la centralità per il buon funzionamento del processo.
La presenza di tecnici altamente qualificati impiegati in attività di gestione e controllo, può essere un fattore determinante in ottica di risultati e competitività.
Flessibilità organizzativa, flessibilità nella produzione e flessibilità nelle prestazioni, all’interno di un contesto di competenze polivalenti, saranno i fattori chiave su cui puntare. Il sistema 4.0 necessita e necessiterà in futuro, nelle figure professionali chiamate a presidiare i processi aziendali, di un’interconnessione dei saperi tra le diverse aree tecniche interessate (meccanica, informatica, elettronica), con una conseguente contaminazione, una significativa attitudine all’interdisciplinarietà e una propensione all’apprendimento continuo.
Per riuscire a cogliere la sfida dell’industria 4.0 le aziende devono dotarsi delle necessarie competenze, rivedendo strategie e pratiche di selezione, assunzione e sviluppo delle risorse umane, ma anche i piani di formazione.
Esistono già significativi esempi di applicazione di tali sistemi a conferma del fatto che la realizzazione di tale “rivoluzione” è già iniziata.
In ogni caso tali applicazioni richiedono e vieppiù richiederanno giovani diplomati e laureati in possesso dei requisiti professionali necessari per affrontare la complessità dei citati innovativi sistemi. Con l’introduzione di macchine sempre più automatizzate si è avuto un superamento dei tradizionali sistemi su cui si basava l’organizzazione della produzione. Le nuove macchine trasformano il contenuto delle mansioni operative: si parla di operazioni di controllo, di manutenzione, con i relativi effetti sul piano delle conoscenze richieste.
Si possono ora analizzare le ricadute economico-tecniche riconducibili all’applicazione di Industria 4.0.
In termini di benefici attesi si parla in primo luogo della possibilità di conseguire una maggiore flessibilità attraverso la produzione di piccoli lotti ai costi della grande scala, con significative ricadute in termini di customizzazione. L’introduzione dell’informatica e del controllo automatico nei processi produttivi permette di disporre di un’organizzazione della produzione capace di adattarsi alla domanda di mercato e di unire i vantaggi della produzione in piccola serie con quelli della produzione in grande serie.
Flessibilità e formazione sono, del resto, due aspetti chiave di industria 4.0.
Un secondo possibile beneficio riguarda una maggiore velocità nel passaggio dal prototipo alla produzione in serie mediante soluzioni tecnologiche innovative. Si può parlare di una maggiore integrazione tra progettazione e produzione.
In termini di acquisti un terzo beneficio è legato alla possibilità di riordinare in modo automatico i beni in esaurimento e di avere transazioni condizionate allo stato effettivo delle consistenze di magazzino.
Un quarto beneficio può derivare da una maggiore produttività conseguibile attraverso minori tempi di set-up (tempo necessario per adattare, sostituire utensili, attrezzature in ordine alle lavorazioni da eseguire), una riduzione degli errori e dei fermi macchina, con aumento dell’affidabilità dei sistemi produttivi e della qualità ottenuta.
Un ulteriore beneficio è collegabile all’ottenimento di una migliore qualità, con la realizzazione di minori scarti grazie all’impiego di sensori che consentano di monitorare la produzione in tempo reale, implementando un controllo sistematico della stessa qualità.
Un altro beneficio ottenibile riguarda la possibilità di una maggiore integrazione delle filiere e catene di fornitura e subfornitura mediante miglioramenti nei sistemi di approvvigionamento e nella logistica, con una più efficiente gestione del magazzino e degli ordini, ottimizzando i rapporti con i fornitori all’interno di ecosisteni collaborativi.
Un altro aspetto positivo può riguardare la sicurezza, nel senso che una migliore interazione e “agilità” di interfaccia uomo-macchina rende possibile una significativa riduzione del numero di errori ed infortuni, un miglioramento delle condizioni di sicurezza e dell’ergonomia del luogo di lavoro.
Un ulteriore elemento positivo concerne la sostenibilità mediante una riduzione dei consumi energetici, delle emissioni, con conseguente riduzione dell’impatto ambientale sull’intero ciclo di vita del prodotto.
La sintesi degli aspetti sopra citati si può concretizzare in un maggiore competitività del prodotto, rivedendo i modelli stessi di approccio al mercato.
Le diverse soluzioni tecnologiche vanno combinate per ottenere risultati che massimizzano i citati vantaggi. Se l’approccio prevalente per avvicinarsi a industria 4.0 è stato prettamente informatico, occorre adottare un nuovo approccio, volto all’integrazione sistemica dei diversi ambiti tecnologici che solo congiuntamente possono assicurare i detti vantaggi.
Di certo la sperimentazione di questi nuovi sistemi richiede notevoli investimenti, ciò che può incontrare dei limiti considerando alcune specifiche caratteristiche del modello industriale del nostro paese, quali ad esempio:
- la presenza di pochi grandi players privati in grado di guidare la trasformazione della ,manifattura italiana,
- un sistema industriale fortemente basato su aziende di piccola-media dimensione, dove soprattutto le aziende più piccole presentano difficoltà e tempi maggiori di adeguamento.
Quanto appena affermato chiama in causa la necessità di specifici interventi statali.
Emerge, in tale contesto, la necessità di definire una sorta di “cabina di regia” del complesso progetto di trasformazione in grado di coinvolgere il settore pubblico e quello privato. Si tratta di un’attività di “regia” che, oltre i ministeri interessati, coinvolga anche le università, i centri di ricerca per lo sviluppo e l’innovazione, il mondo economico ed imprenditoriale, le organizzazioni sindacali più rappresentative.
In questo contesto il piano nazionale industriale 4.0, elaborato per il periodo 2017 – 2020 evidenzia un insieme di interessanti direttrici di intervento. Gli obiettivi prioritari del piano sono quelli di favorire l’ammodernamento del parco beni strumentali e la trasformazione digitale delle aziende manifatturiere italiane.
Appare particolarmente interessante la prevista implementazione di un Piano nazionale per la scuola digitale. Nello specifico si prevede una focalizzazione su percorsi di alternanza scuola-lavoro coerenti con industria 4.0, una specializzazione di corsi universitari e master sulle tematiche in oggetto in partnership con player industriali e tecnologici, un ampiamento dell’offerta formative su tematiche industria 4.0 per gli studenti degli Istituti Tecnici Superiori, un incremento dei dottorati di ricerca su tecnologie industria 4.0, la creazione di selezionati Competence Center a livello nazionale, un adeguamento continuo delle competenze mediante i fondi interprofessionali.
L’insieme di queste misure è ambizioso, prefigurando una trasformazione della struttura produttiva, una digitalizzazione delle imprese e dei processi di formazione. Per le aziende italiane, anche grazie ai contributi citati, emerge un forte incentivo ad investire per essere più competitive in un mercato sempre più globale.
A cura di: Marco Giannini
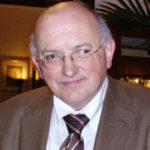
Marco Giannini è Professore di Organizzazione Aziendale presso il Dipartimento di Economia & Management dell’Università di Pisa. Ha partecipato a numerosi progetti di ricerca concernenti innovazioni organizzative, evoluzione dell’organizzazione del lavoro, gestione del personale, sicurezza sul lavoro.