Lean Design: la gestione della varietà dei prodotti e dei servizi
In ottica di “progettazione snella” (Lean Design), il tema della gestione della varietà riveste un’importanza fondamentale per la ricaduta che la stessa ha sia in termini di soddisfazione del cliente, sia in termini di costi di produzione dei prodotti e di erogazione dei servizi.
Il Variety Reduction Program (VRP) è una tecnica, teorizzata da Koudate e Suzue nel 1992, che ha per obiettivo la riduzione dei costi di progettazione e sviluppo-prodotto, limitando il numero dei componenti e dei processi necessari per fabbricare un prodotto, rispondendo contemporaneamente alla richiesta del mercato di un’elevata varietà di prodotti. In altri termini, non deve sembrare paradossale adottare una tecnica di riduzione della varietà in un contesto di soddisfazione del cliente e quindi di ampiezza di gamma e personalizzazioni: trattasi infatti della riduzione della varietà interna (che, per un’azienda, significa costi) a parità di varietà esterna, cioè offerta al mercato (varietà quest’ultima che contribuisce alla soddisfazione del cliente).
Per quanto sia in atto un marcato ripensamento su un’eccessiva varietà esterna (in fin dei conti, la varietà di Apple o Ikea è molto meno ampia di quanto potrebbe essere) ovvero viene messo in discussione che molta varietà determini in sé molta più soddisfazione del cliente, non vi sono dubbi che la riduzione della varietà interna (vuol dire: costi) è molto importante negli attuali contesti competitivi, caratterizzati da un’elevata dinamica d’introduzione di nuovi prodotti o nuove versioni, con conseguente aumento della complessità gestionale e produttiva dovuta alla numerosità dei componenti e alle loro diverse combinazioni, in altri termini costi derivanti dalla varietà.
Vengono considerati tre diversi tipi di costi, molto diversi dai costi tradizionalmente annoverati nel controllo di gestione, questi ultimi trattandosi tipicamente di costi classificati per natura (dei materiali, delle macchine/impianti, del personale, ecc.), per variabilità (fissi, variabili, semi-variabili, ecc.), per attribuzione a un centro o a un prodotto (diretti/indiretti), in relazione al tempo (preventivi, correnti, consuntivi), ecc. I costi considerati dal VRP sono:
- i costi funzionali, legati a specifiche prestazioni/funzioni che il prodotto deve svolgere (indicano il costo per assicurare una certa prestazione oppure funzione aggiuntiva al prodotto, derivante dalla necessità di prevedere diversi materiali, componenti, processi produttivi, ecc.). Il legame tra prestazioni/funzioni e costo di prodotto è studiato dall’Analisi del Valore (“Value Analysis”);
- i costi della varietà, imputabili al fatto che un’ampia gamma di prodotti, se da un lato può essere motivo di apprezzamento dal mercato, dall’altro richiede normalmente lavorazioni diverse e quindi l’impiego di macchine e attrezzature dfferenti;
- i costi del controllo, ovvero la valutazione economica della complessità gestionale.
I suddetti costi hanno andamenti differenti in relazione al grado della varietà stessa: gli ultimi due sono crescenti all’aumentare della varietà dei prodotti e dei processi; i primi, invece, sono decrescenti. Infatti, una maggiore varietà permette di distribuire i costi delle funzionalità su più prodotti: si pensi al costo di accessori che possono essere montati su famiglie di prodotti differenti, a seconda degli allestimenti di ciascuno. La tecnica consente la ricerca del livello di varietà che deve essere presente per minimizzare la somma dei tre costi. Si tratta quindi di una logica di considerazione dei costi alquanto innovativa rispetto ai tradizionali approcci contabili.
La varietà esterna è nota come ampiezza di gamma (“range” di prodotti all’interno del quale il consumatore può scegliere), mentre la profondità di gamma misura il numero di opzioni di prodotto possibili all’interno di una certa “famiglia” di prodotti (ad esempio: versioni a 3 o 5 porte, allestimenti business o luxury, ecc.).
La varietà interna può invece essere misurata attraverso “indici di varietà” quali:
- il “parts index”, che tiene conto dei diversi tipi di componenti che compongono un prodotto e della loro numerosità;
- il “production process index”, che tiene conto dei diversi tipi di processi occorrenti per realizzare un prodotto e del numero di macchine coinvolte in ogni processo.
Utilizzando questi indici e i suddetti costi – funzionali, della varietà e del controllo – è possibile avviare programmi per la riduzione della varietà, combinando opportunamente i componenti e minimizzando il numero di componenti necessari per svolgere una funzione del prodotto. Le valutazioni di costo conducono a predefinire un grado di varietà prossimo al punto di minimo della curva (ad “U”) somma dei tre costi.
Vengono proposte come modalità per la riduzione della varietà (interna):
- la distinzione tra parti fisse e parti variabili. In qualsiasi progetto bisognerebbe suddividere chiaramente tutte le parti in parti fisse e parti variabili (in relazione alle esigenze del cliente), eventualmente prevedendo delle parti semi-variabili (simili), e bisognerebbe cercare di aumentare in numero le sole parti variabili che rispondono a reali specifiche esigenze dei clienti, riducendo gli “accessori” superflui;
- l’utilizzo della combinazione di parti, sia per ampliare la diversificazione dei prodotti sia per realizzare funzioni di livello superiore attraverso più funzioni di livello inferiore;
- l’applicazione della multifunzionalità/integrazione, facendo svolgere a un solo componente/sotto-assieme più funzioni (ad esempio, affidare a un unico albero motore rotante sia la trasmissione del movimento della distribuzione che quello per la pompa dell’olio e per il climatizzatore), eventualmente integrando più componenti in uno solo;
- l’analisi del “range”, ovvero definizione dell’ambito delle prestazioni coperte da un certo componente, senza doverlo sostituire con un altro, al fine di ridurre il numero dei componenti da progettare/produrre pur coprendo tutti i “range” necessari;
- analisi della “serie”, ovvero ricerca di rapporti costanti (diversi per ogni serie) tra due dimensioni, o tra due prestazioni, o tra dimensioni e prestazioni.
Inoltre, la riduzione della varietà interna dovrebbe essere attuata in modo da avere bassi “production process index”, quantomeno nelle operazioni iniziali. Quindi, a parità di varietà esterna offerta al mercato, misurabile nell’ultima fase produttiva (tipicamente di assemblaggio), la varietà andrebbe spostata il più possibile a valle, verso appunto le operazioni terminali. È questo il concetto del fungo (“mushroom concept”), in cui al limite la differenziazione avviene solo nelle ultime operazioni (il cappello del fungo), rimanendo poche e standard tutte quelle precedenti (il tallo del fungo). Quindi, la riduzione della varietà interna a parità di quella esterna, viene affiancata dallo spostamento di essa verso le ultime operazioni del ciclo, secondo il concetto di fungo.
Fra i programmi di riduzione della varietà, trova un suo spazio autonomo la modularizzazione o progettazione di tipo modulare. Essa consente di ottenere prodotti sufficientemente differenziati unitamente ad economie nelle attività di progettazione, produzione e gestione dei flussi logistici, grazie a un utilizzo ripetitivo di moduli e componenti standard nella definizione del prodotto (in giapponese: “Henshu Kaihatsu” o sviluppo modulare).
La modularizzazione viene operata sulla distinta base, e può essere di tipo verticale oppure orizzontale. Nel primo caso, vi è una parte fissa comune a diversi prodotti (per questo, detti “core products”) e la differenziazione trae origine dal montaggio di parti variabili (ad esempio, accessori) sui “core products”: i prodotti, quindi, vengono a diversificarsi sulla base dei “core products”, costituendo delle “famiglie di prodotti”. Nel secondo caso, la varietà deriva dalla combinazione di moduli base, che portano a dei moduli intermedi (anche detti “gruppi funzionali”), che variamente accompagnati determinano a loro volta i prodotti finiti: questo tipo di modularizzazione si definisce orizzontale in quanto non vi è nessuna prevalenza, nel prodotto, di una parte.
Articolo a cura di Stefano Tonchia
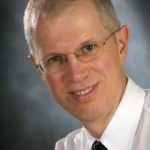
Professore Ordinario di “Organizzazione Aziendale e Lean Management” e di “Innovation & Project Management” all’Università di Udine.
E’ autore di 7 libri per Il Sole 24 Ore e di 3 testi in inglese (compreso “Industrial Project Management” per Springer – nuova edizione 2018).
E’ formatore, consulente e advisor di Aziende leader.